3D-Druck ist populär, und Drucker für den Heimgebrauch sind billiger geworden. Für den Elektroniker hat diese Technik viel zu bieten: Mechanische Kleinteil wie z.B. Gehäuse, Zahnräder, Seilrollen und ähnliches können im Handumdrehen selbst hergestellt werden. Das klingt so gut, dass es an der Zeit ist, die Technik selbst auszuprobieren.
Um es vorweg zu nehmen: Im Handumdrehen geht bei der 3D-Druckerei gar nichts. Der Weg vom Modell zum fertigen Produkt ist weit. Aber die Resultate können überzeugen!
Geeetech Prusa I3 X
Für meine ersten Versuche bestellte ich mir einen Bausatz der chinesischen Firma Geeetech, basierend auf dem quelloffenen FDM 3D-Drucker Prusa I3, ein einfaches und zuverlässiges Konzept, das sich bewährt hat. Geeetech ist einer von vielen Herstellern, die Prusa I3-Nachbauten anbieten.
Etwa eine Woche nach der Bestellung kam das Paket an. Es enthielt auf zwei Styropor-Lagen verteilt eine Unzahl von kleinen und großen Bauteilen, die alle gut geordnet und sorgfältig durchnummeriert waren. Per Email erreicht mich ein Link zu der PDF-Bauanleitung auf dem Geeetech-Server.
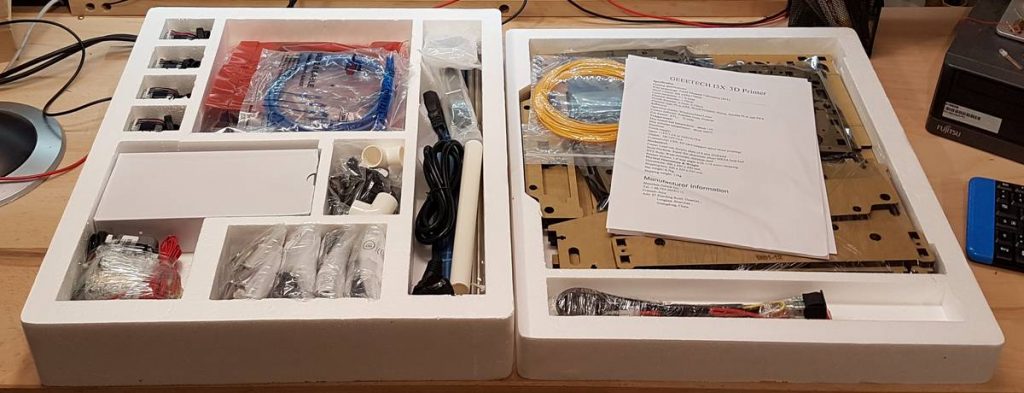
Für den Zusammenbau sollte man sich Zeit nehmen. Laut Geeetech ist der Nachbau in 11 Stunden möglich. Davon würde ich abraten. Ich selbst habe 5 Tage benötigt, wobei ich jeden Tag 3 oder 4 Stunden investieren konnte. Die englischsprachige Anleitung ist gut gemacht und erklärt die Schritte mit vielen Bildern. Darüber hinaus gibt es einen Satz von YouTube-Videos, die alles ausführlich zeigen.
Der Rahmen des Geräts besteht im Wesentlichen aus 8 mm starken, schwarzen Acrylplatten. Die Teile sind exakt geschnitten. Ob das schwarz-glänzende „Klavierlack-Finish“ für den Einsatz in der Werkstatt optimal ist, sei dahingestellt. Die Schrauberei ging bei guter Passgenauigkeit der Teile zügig voran. Zum Glück sind viele der Kleinteile in der Überzahl enthalten, so dass es kein Problem war, wenn ein kleines Schräubchen nicht mehr auffindbar war.
Allerdings scheinen einige Details ständig überarbeitet zu werden, so dass es immer wieder Abweichungen zwischen den Bildern und den tatsächlich vorhandenen Bauteilen gab. Insgesamt benötigte der Zusammenbau aktives Mitdenken und ein gutes technisches Verständnis. Leider fehlt eine gute Übersichtsbeschreibung des Gerätes mit Markierung der einzelnen Komponenten (in früheren Zeiten gab es so etwas als „Explosions-Zeichnung“), so dass ich streckenweise Bauteile zusammensetzte, ohne ihre Rolle zu verstehen. Wenn man dann etwas falsch zusammengesetzt hat, ist das aber kein Problem, weil alle Komponenten verschraubt sind und wieder gelöst werden können.

Es gab eine Hürde, die ich nach Bauanleitung nicht lösen konnte: Die Z-Achse machte Probleme. Während die X- (links/rechts) und Y- (vorne/hinten) Achsen durch Zahnriemen gesteuert werden, was auf Anhieb gut funktionierte, wird die Z-Achse (oben/unten) durch Gewindestangen bewegt. Nach dem ersten Zusammenbau saßen die Gewindestangen so fest, dass sie sich absolut nicht mit den Motoren drehen ließen. Die 8 mm Führungslöcher in den entsprechenden Plastikteilen waren genau auf Größe geschnitten und ließen der M8-Stange keine Luft. Zur Behebung des Problems wurden die Löcher direkt am Schlitten und an der oberen Platte auf 10 mm aufgebohrt.
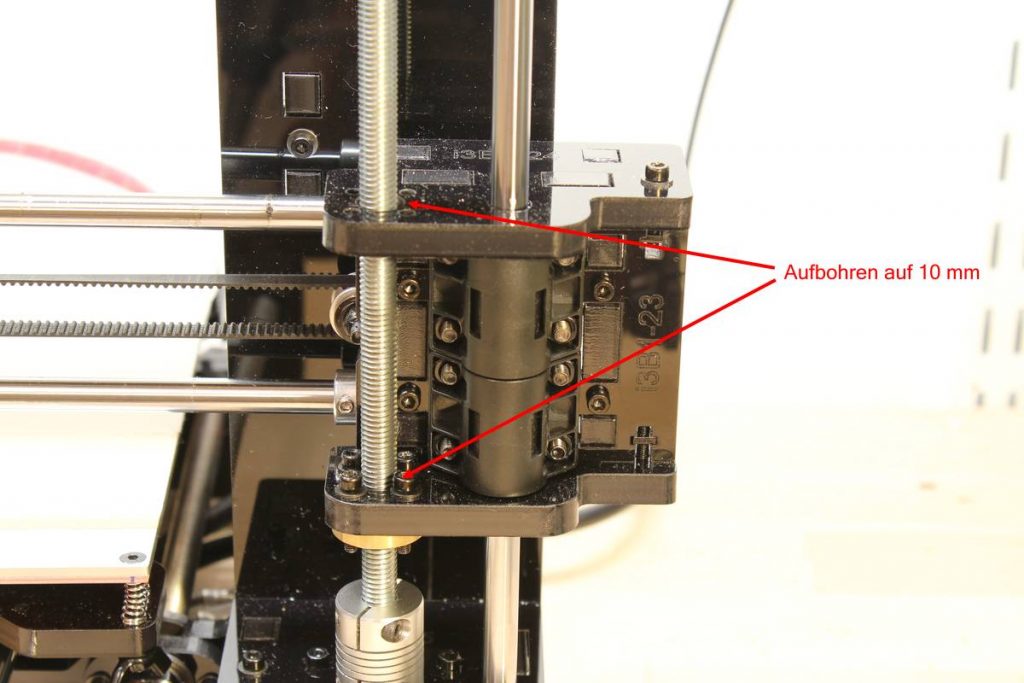
Da die Gewindestange jetzt keinen zuverlässigen Halt mehr hatte, setzte ich zur Stabilisierung auf die obere Platte jeweils ein Kugellager mit 8 mm Innendurchmesser. Dadurch war eine reibungsfreie Lagerung bei präziser Führung gewährleistet. Ähnliche Ansätze mit 3D-gedruckten Konstruktionen werden in den Foren diskutiert (Stichwort z axis wobble fix). In meinem Fall fiel die Wahl auf Sperrholz, weil ich eine Lösung brauchte, bevor der Drucker funktionsfähig war.
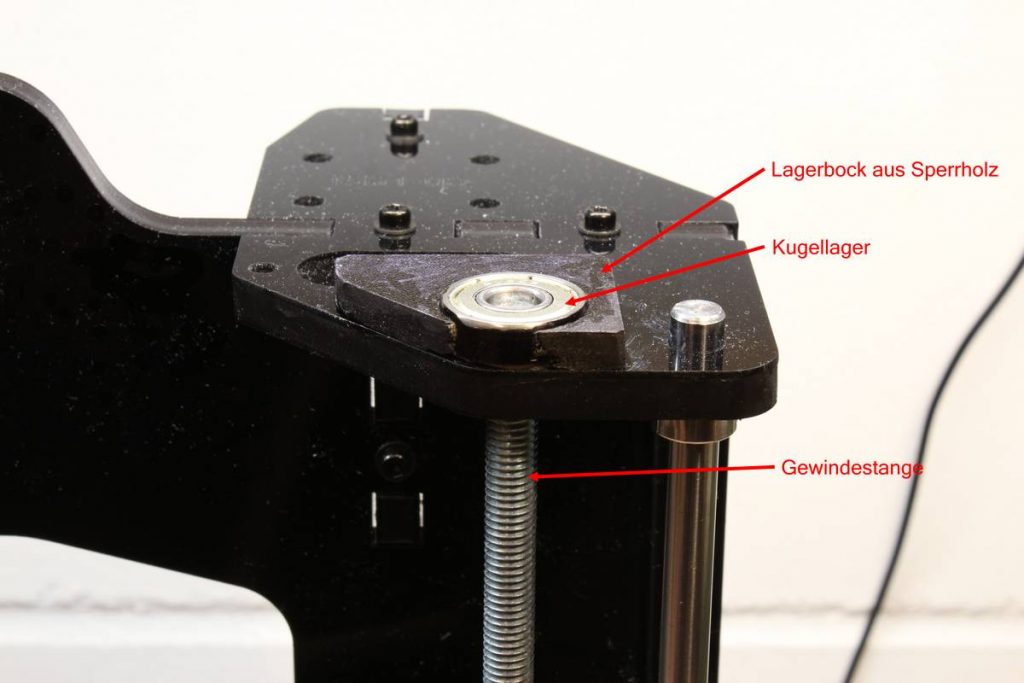
Außerdem hatte eine der beiliegenden Gewindestangen einen deutlichen Schlag und wurde durch eine Stange besserer Qualität aus dem Baumarkt ersetzt. Mit einigen wenigen Tropfen harz-freiem Öl an der Gewindemuffe auf der Gewindestange lief der Antrieb dann reibungsfrei.
Zum Abschluss wurde alle Komponenten elektrisch verbunden durch eine Vielzahl von Steckverbindungen – genau nach Bauanleitung. Wieder musste ich mich damit auseinander setzten, dass einige Details der Controller-Platine von der Beschreibung abwichen. Trotzdem war alles logisch und nachvollziehbar angeordnet.
Inbetriebnahme
Geeetech stellt ein zweites Dokument bereit, das User Manual, das die Inbetriebnahme und das Fine Tuning beschreibt. Bevor es zum Einschalten ging, musste die zugehörige Software auf dem steuernden PC installiert werden. Geeetech verwendet Repetier Host, ein gut etabliertes Open Source-Programm. Tatsächlich verlief die Installation auf meinem Windows 10-PC völlig problemlos.
Dann kam der spannende Moment: Strom ein! Aber kein Grund zur Aufregung. Die Verbindung zwischen PC und Controller-Board funktionierte sofort, und die Drucker-Funktionen ließen sich gut steuern. Vom PC aus lassen sich alle Achsen manuell ansteuern. So konnte ich auch die problematische Z-Achse ausprobieren und nachjustieren, bis es reibungslos lief.
Dann aber gab es Probleme beim Heizen des Extruders. Zwischenzeitlich zeigte das Geräte die „MINTEMP“-Fehlermeldungen, was bedeutet, dass der Thermistor einen Temperaturwert unter 19 Grad erfasst. Anscheinend hatte der Thermistor im Alu-Block des Extruders keinen zuverlässigen Kontakt mit dem Board. Eine genauere Analyse ergab, dass die kleinen Steckverbinder am Alu-Block keine stabile Verbindung hatten. Die Kontakte befinden sich unter gelben Klebeband und sind deshalb nicht so leicht zu finden. Nachdem ich sie mit einer Zange nachgedrückt hatte, lief alles nach Plan. Das Klebeband habe ich inzwischen durch zwei Kabelbinder ersetzt. Übrigens konnte ich meinem Impuls, die Verbindungen mit dem Lötkolben dauerhaft zu machen, widerstehen. Das Problem dabei ist, dass die Lötstellen bei Temperaturen oberhalb von 200 Grad nicht halten. Also lieber klemmen!
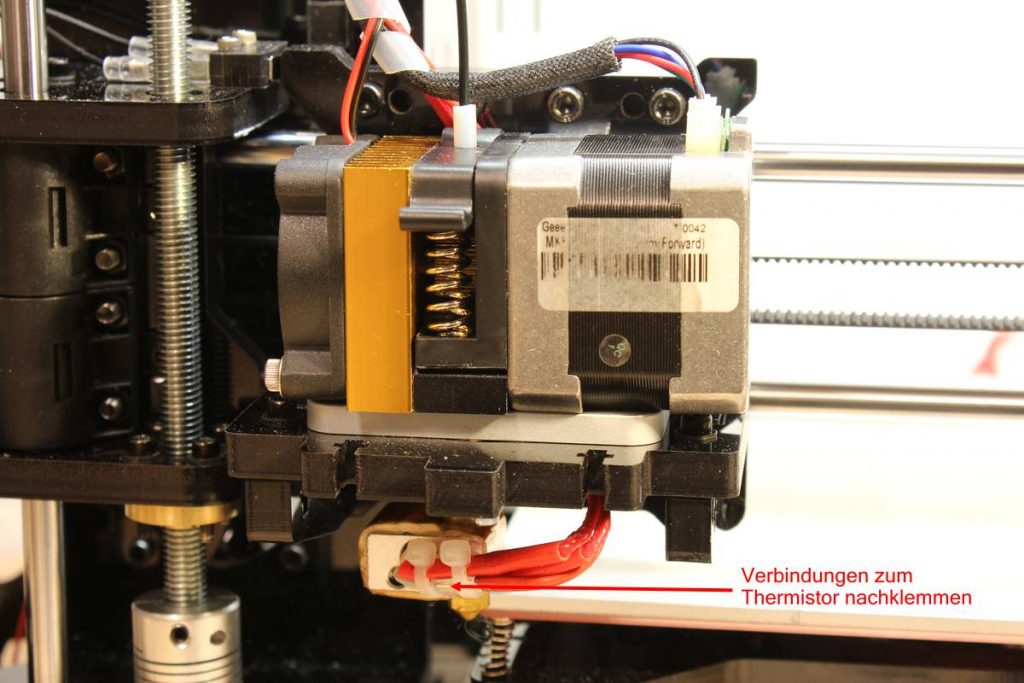
Zum Schluss musste noch das Druckbett nivelliert werden, was nach der Anleitung gut machbar war.
Dann konnte es losgehen. Geeetech legt 3 Meter gelbes Filament in den Karton. Der erste Versuch, einen runde Scheibe zu produzieren, die als *.stl-File auf dem Geeetech-Server bereitsteht, war weitgehend erfolgreich. Prima. Was kommt als nächstes?
Tool Chain
Sinn und Zweck des Druckers in meinem Elektronik-Labor ist es, nützliche Kleinteile für meine elektrischen Geräte zu produzieren. Der nächste Schritt ist also eine Software, die die Erstellung solcher Bauteile am PC ermöglicht. Meine Wahl fiel auf FreeCAD, ein beeindruckendes, wenn auch leider nicht ganz fehlerfreies Programm, um 3-dimensionale Objekte zu designen. Auch dieses Programm braucht etwas Einarbeitungszeit. Zum Glück gibt es sehr hilfreiche YouTube-Tutorials, die die Grundlagen gut erklären. Man sollte sich aber Zeit nehmen.
Die Ausgaben von FreeCAD sind nicht ohne weiteres mit dem Drucker kompatible. Die Körper sind z.B. mit papier-dünnen Wänden definiert und nicht „wasserdicht“ (mannigfaltig). In der Regel muss noch ein Mesh erzeugt werden, das die Körper füllt. Zwar kann FreeCAD auch diesen Schritt übernehmen. Ich habe aber besser Erfahrungen mit dem ebenfalls freien Programm Meshmixer von Autodesk gemacht. Dort lässt sich über die Funktionen edit -> solid fill ein Körper erzeugen, der dann direkt vom Repertier Host importiert und zum Druck geschickt werden kann.
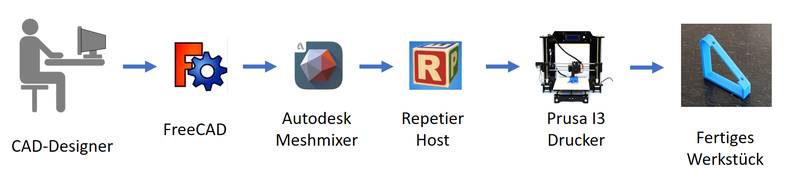
Ein weiteres praktisches Problem ergab sich dadurch, dass manches Mal der erste gedruckte Layer nicht recht auf der Alu-Fläche des Druckbettes halten wollte. Wenn der erste Layer nicht stabil liegt, dann endet der Druck über kurz oder lang im Chaos. Das ist ein viel diskutiertes Thema in den Internet-Foren. Dort fand ich auch Abhilfe: Eine Schicht Tesa Abdeckband für Maler (wieder aus dem Baumarkt meines Vertrauens), das ohne Lücke oder Überlapp auf die Alu-Platte geklebt wird, erhöht die Haftung. Wenn die Nivellierung stimmt, dann hält die erste Schicht absolut fest. Das Band ist Verbrauchsmaterial und musste nach ein paar Ausdrucken erneuert werden.
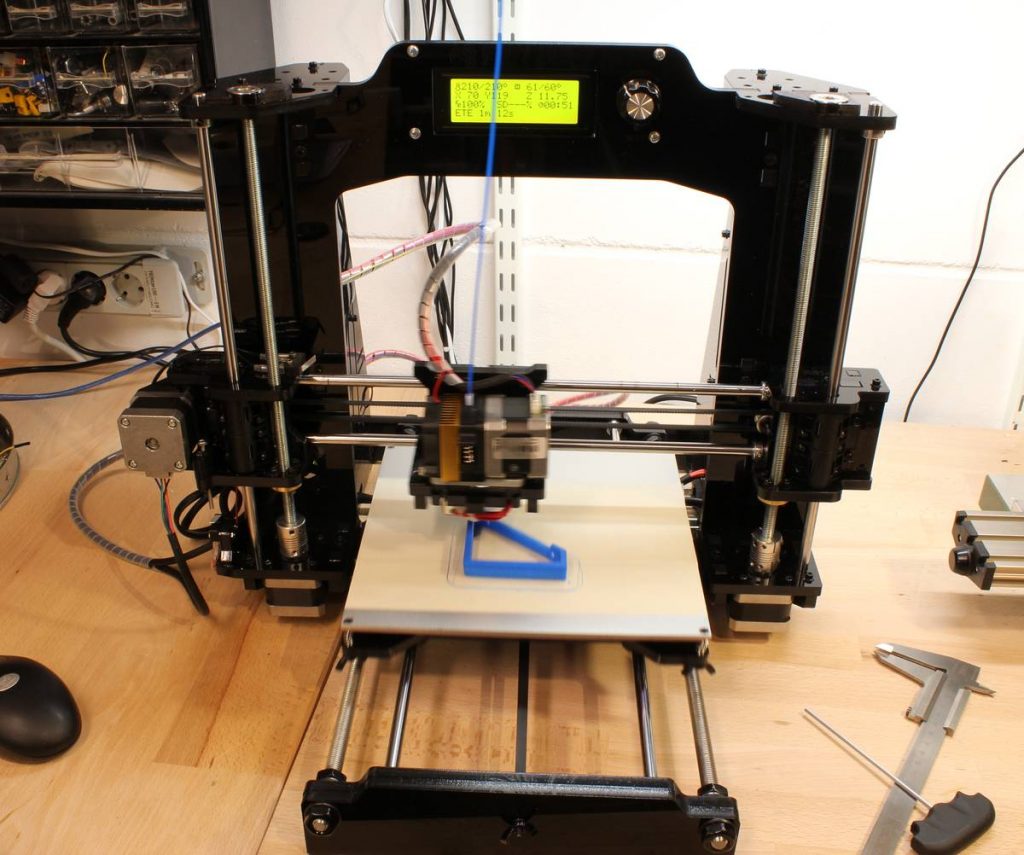
Endlich 3D drucken!
So, jetzt konnte es endlich losgehen. Als eines der ersten Objekte produzierte ich Halter für das Graphik LCD-Display, mit dem ich oft arbeite, so dass das Display bei meinen Experimenten nicht mehr lose auf dem Arbeitstisch liegen muss. Für eine bessere Druckqualität habe ich die Druckgeschwindigkeit etwas heruntergesetzt. Auch mit der Temperatur des Extruders kann man experimentieren. Die Zahl der Parameter zur Feinabstimmung ist groß und braucht Geduld und Experimentierfreude. Das Resultat ist dann aber wirklich sehr schön und ein wohlverdienter Lohn der Mühe!
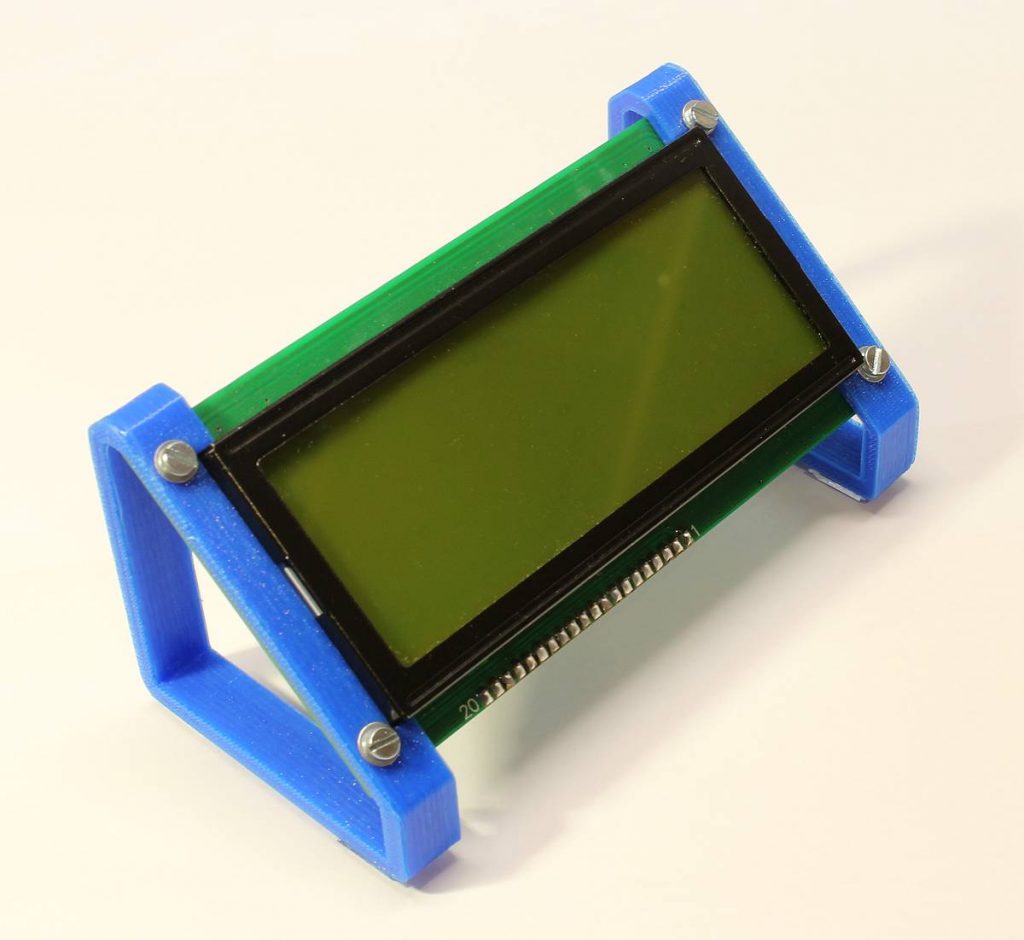
Es ist sehr erfreulich, wenn man dann das fertigen Bauteil vom Druckbett löst und ohne weitere Bearbeitung – keine Löcher bohren, keine Ausschnitte nachfeilen – an das Display schraubt.
Fazit
Der Geeetech Prusa I3 X ist gut geeignet für den Einstieg in die 3D-Druckerei. Der Bausatz ist durchdacht und bietet gute Qualität, wenn auch einige Details angepasst werden müssen. Die Bauanleitung beantwortet nicht alle Fragen, so dass Mitdenken, technisches Verständnis und gelegentliches Stöbern in einschlägigen Foren gefordert sind.
Der Einstieg in das Thema benötigt viel Zeit. Es ist sicherlich kein Consumer-Produkt, das nach Aufstellen und Einschalten bereits gute Ergebnisse produziert. Hier sind mehr Investitionen vom Anwender gefragt. Wenn man die Hürden aber genommen hat, dann eröffnet der Drucker enorme Möglichkeiten und belohnt den Anwender mit guter Qualität.
Mehr gedruckte Objekte werden folgen!
Download
FreeCad und konvertiertes STL-File für den Display-Halter: DisplayHalter
Hallo,
ich selber habe 2 Ender3 in Benutzung, bei einen mußte ich die obere Lagerung der Z- Gewindestange
durch „Veredeln“ der Bohrungen zu Langöchern korrigieren, die Stange selbst war ok.
Na ja, man bekommt halt den realen Gegenwert zum Preis, billig heißt eben Nacharbeit.
Als Druckunterlage sind die schwarzen buildtak-Nachahmungen aus China recht gut. Aufgeklebt
auf passende kupferlose FR4-Platte (beides 235×235 mm im www erhältlich) kann man mit den
Klammern aus dem Bürobereich mit der ALU-Platte verbinden. Zum Ablösen bei sehr fest haftenden
Druckgut nimmt man die Platte in die Hand und kann durch Biegen oft ein Abspringen bewirken, sonst muß eine scharfe Klinge ran. Die Druckermechanik wird dadurch nicht unnötig belastet, ein
Leveln des Bettes ist seltener nötig.
Als CAD-Programm kann ich nur ViaCad 3d empfehlen, kostet zwar Geld, die Ausgabe habe ich nicht bereut. Danke für die guten Informationen zur Grafik – Display – Ansteuerung. Ich melde mich da
auf jeden Fall wieder. Bleib gesund ! Viele Grüße von Uwe (DL5KU)